
The textile industry is one of the most polluting. It is a fact, and no, we are not throwing stones at our own roof, we are simply aware of the bad practices that take place in this industry and our mission is to reverse that situation. We want to make the world a better place without neglecting a trade that has lasted almost half a century, and we firmly believe that both things are compatible.
Thanks to our determination to reduce our impact on the environment, we have developed Greensight. Thanks to it, among other things, we managed to save up to 90% of water in our production.
_What is Greensight technology
After years of research and a lot of effort, we have managed to combine different techniques that allow us to be a respectful brand with our environment. We have united this set of techniques under the same umbrella called Greensight.
Greensight is a sustainable production process that consists of working with biomass, dyeing the jeans with nebulization, washing them with ozone and finishing them with laser finish technology.
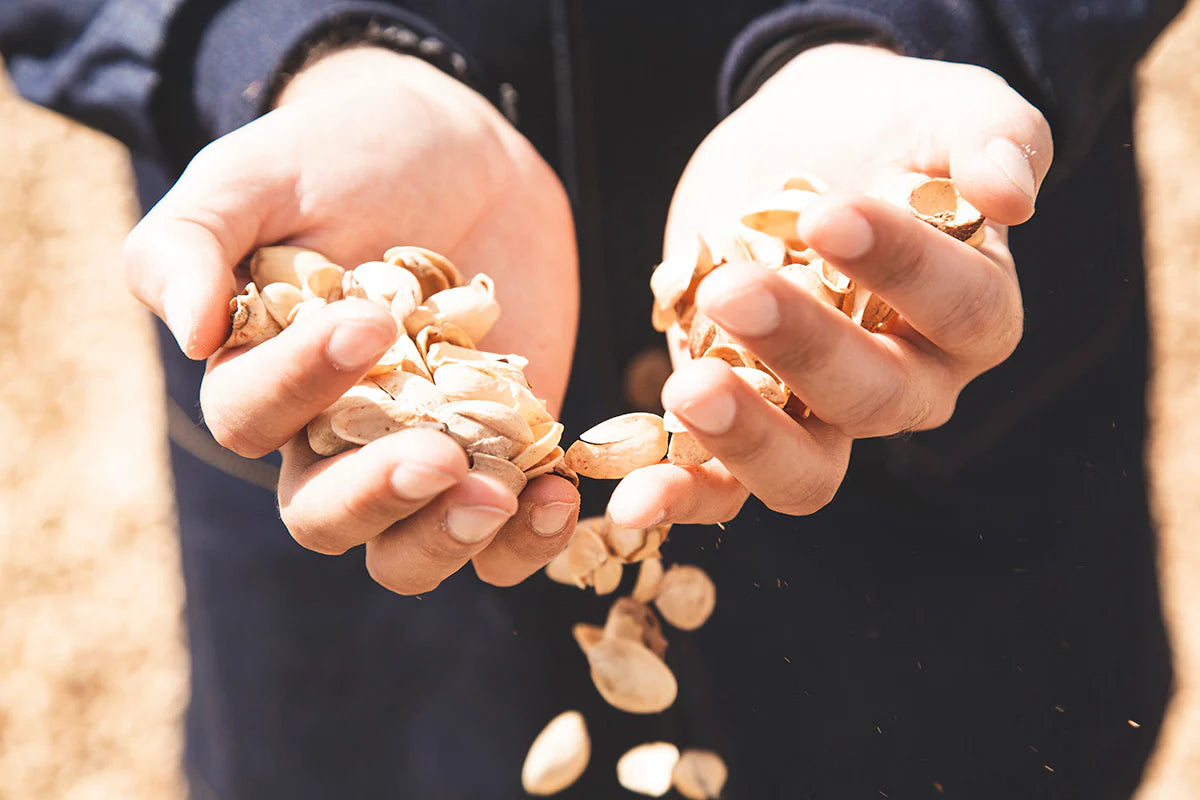
biomass
Biomass is one of the most sustainable energy sources. In addition, it is a source of energy considered Carbon Neutral, since the CO2 that is released when burning organic remains are the same as those that the plant has absorbed during its life.
Depending on the time of year or the season, we use different fruit surpluses: olive pits, pistachio shell, almond or peach pit, among others, as fuel for our machines. As we work in a rural environment where agriculture plays an important role, all our organic waste supply is local, so we reduce emissions in its transport.
Approximately, to make a pair of jeans, we need the energy generated from 2kg of almond shells.
misting
Once the garment has been made, it is time to dye it since, depending on the fabric, there are pants that are sewn in an ecru color. To carry out this process in the traditional way, water is the main transmission vehicle where it is mixed with the dye and the garments are bathed until the desired color is achieved. In fact, to be able to dye 1kg of pants, 12 liters of water are needed. With Nebulization or Eco Finish technology, we replace water with air, so that the dye is evenly impregnated in the pants. Thus, we only need 1 liter of water for 1kg of jeans.
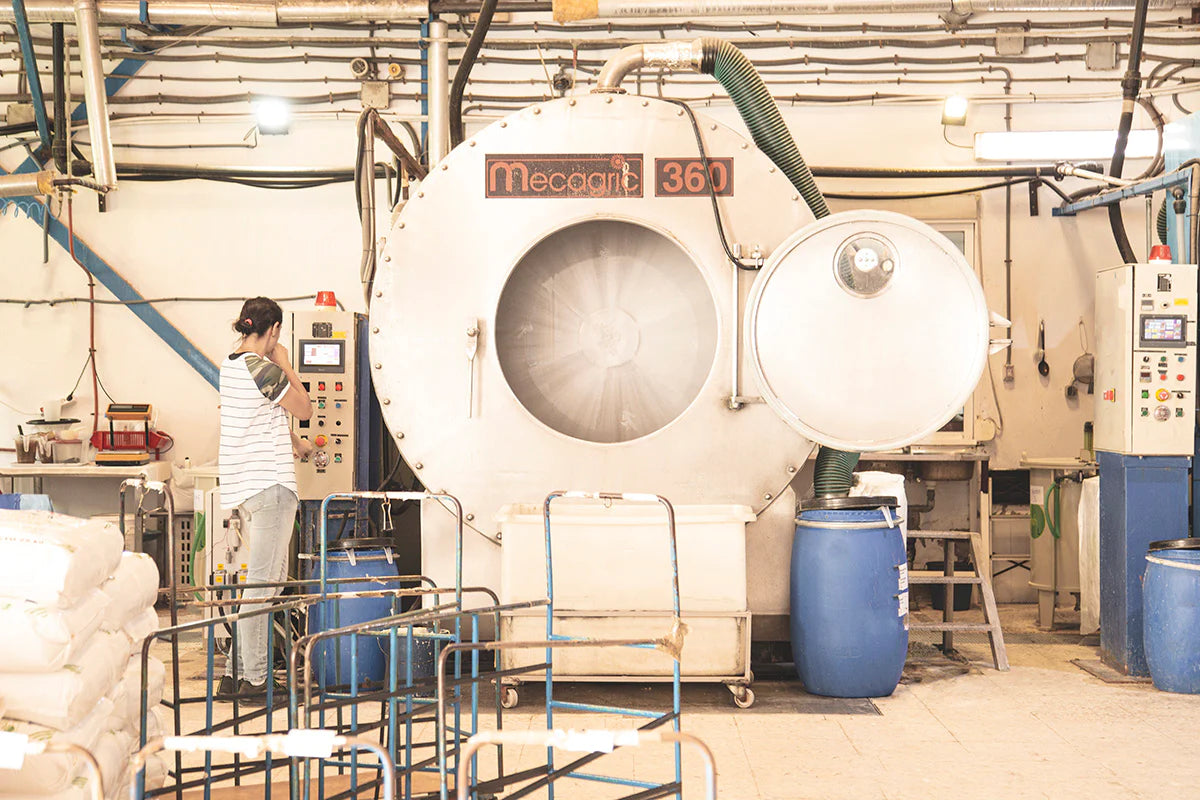
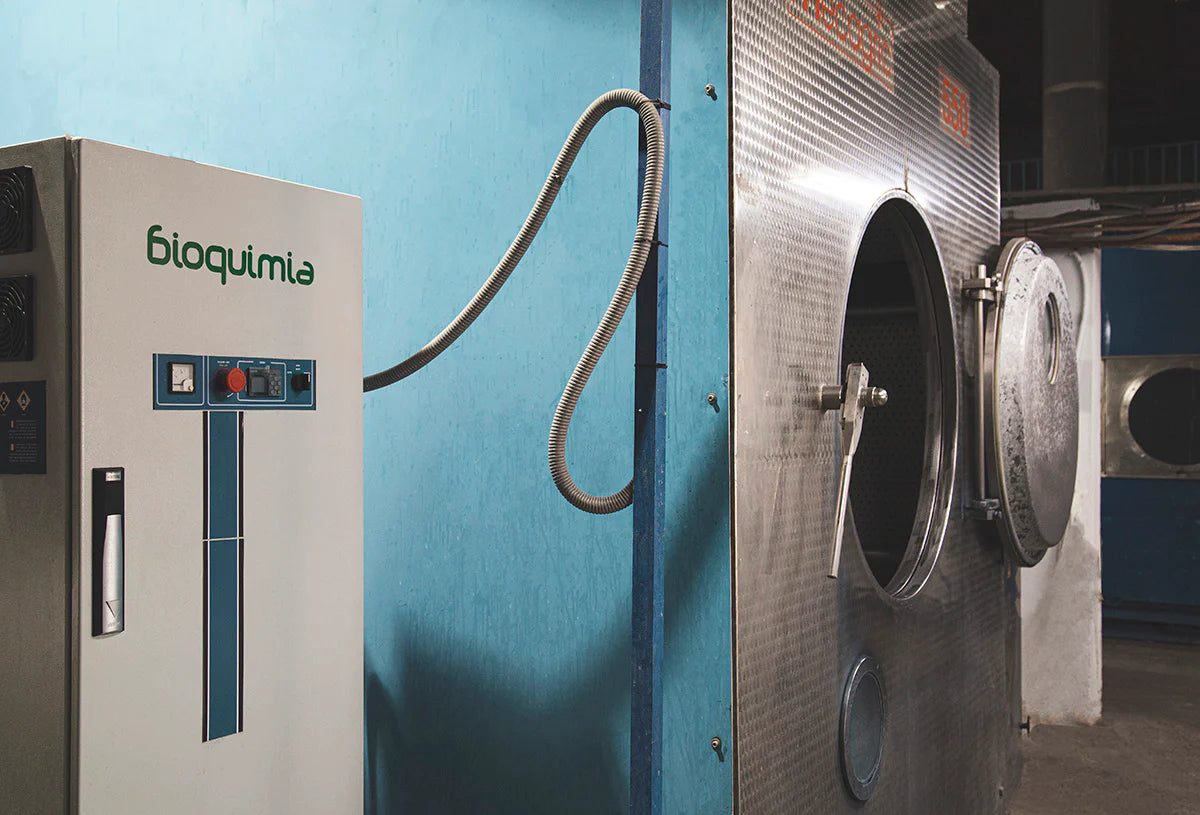
Ozone
Did you know that to make jeans in the traditional way you need all the water a person would drink in 7 years? Upon knowing this comparison, we got to work to avoid so much waste of water and after several studies and tests we managed to incorporate ozone washing.
This process needs less than half the water, specifically it can work with 54% less water and achieve the same results as if done traditionally. But ozone not only has the advantage of saving water in the production process, but also requires less execution time. With ozone washing we manage to save 80% of time and that translates into a reduction in energy.
Lastly, ozone is a natural oxidant, so our jeans are washed with clean production processes, reducing the use of chemicals.
laser finishing
One of the final processes in making pants, especially jeans, is the wear finish. Traditionally, these finishes were made with sandpaper or sand, both of which are harmful to the health of the person performing the work and also have a negative impact on the environment. To deal with these two problems, we use laser technology, a clean energy that does not use chemicals and does not affect the health of our workers. It is very quick to apply and offers us a wide variety of applications.
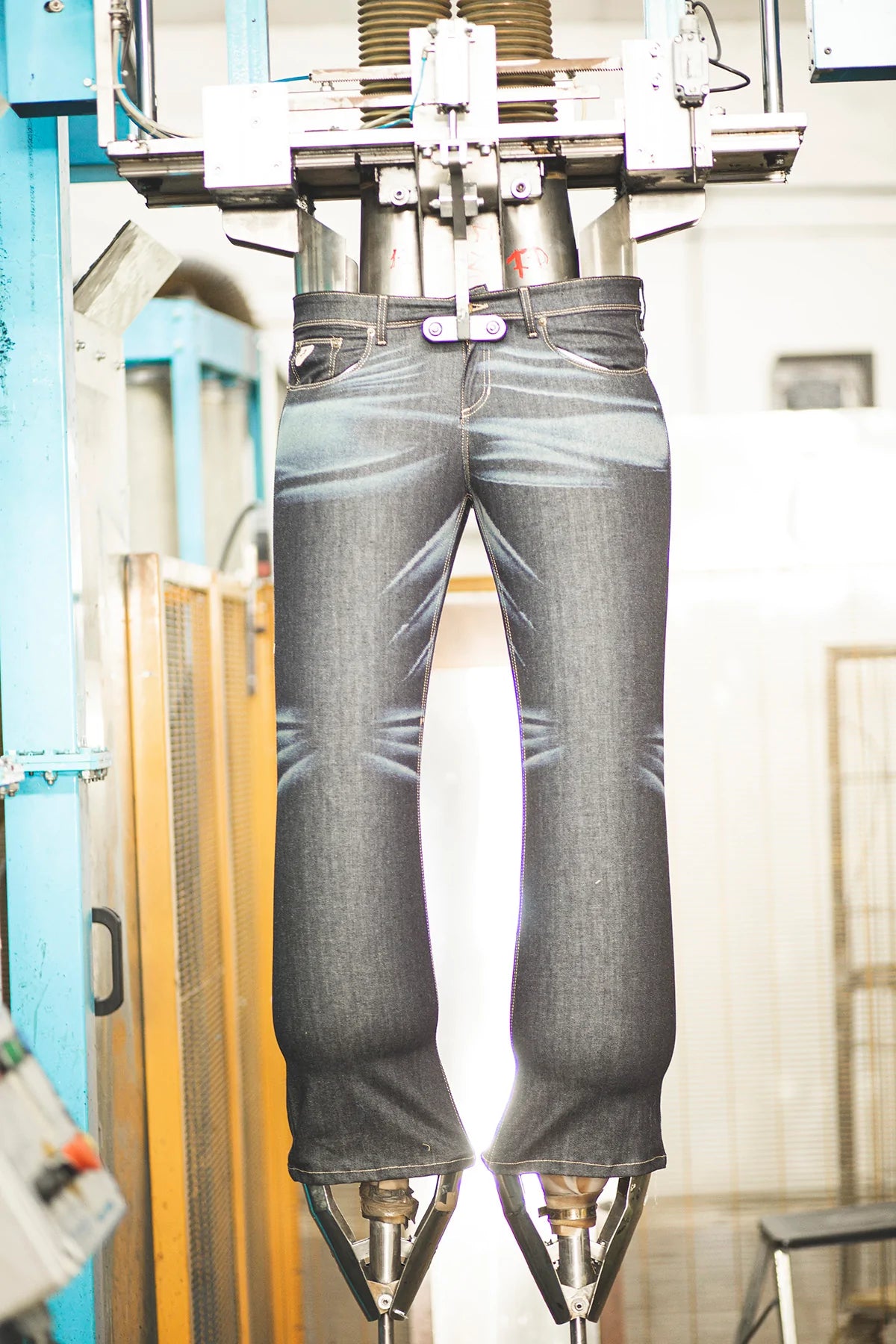
This does not stop here, as Greensight is one of the small changes that we still have to make. Later we will explain to you what a new low environmental impact project that we are carrying out, called Neo-Recycling, consists of. At Captain Denim we are very proud of being able to work with the minimum amount of resources that harm the planet.